TITANS OF NUCLEAR
A podcast featuring interviews with experts across technology, industry, economics, policy and more.
Latest Episode
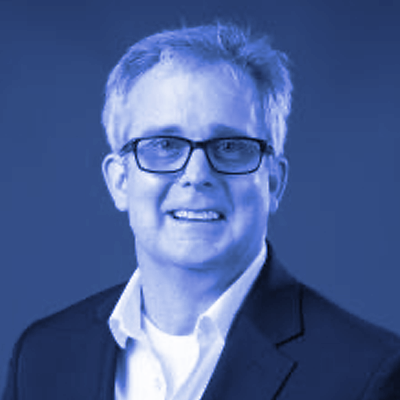
1) The beginning of Brian’s career and his time in the United States Navy as a diver, as well as what drew him to engineering and nuclear
2) Brian’s initial journey to Oregon State and all of the research projects he’s had a hand in since then
3) Fostering a passion for nuclear in the next generation of nuclear engineers and why the researchers as just as important as the research itself
4) What challenges and successes the nuclear industry will face in the coming years and how to form your individual opinion on nuclear energy
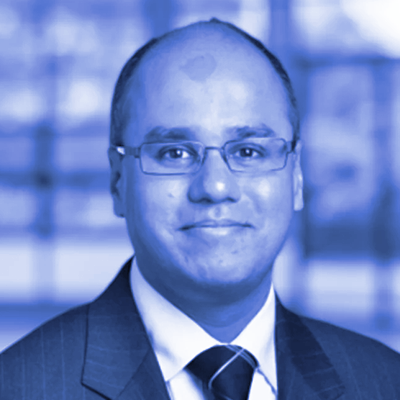
1) Anurag’s background in mechanical engineering and his personal journey in the nuclear industry
2) The financial risk profile of a nuclear plant versus that of other energy sources
3) KPMG’s work improving nuclear’s ability to stay on time and on budget and how that benefits public perception of the nuclear industry
4) How small modular reactors can streamline production, decrease cost, and increase nuclear scalability
1 - Introduction to Nuclear Financing
Bret Kugelmass: How did you first start working in the nuclear sector?
Anurag Gupta: Canada, especially Toronto, has a vast expertise in civil nuclear. Canada has harnessed nuclear power to provide citizens with a source of clean energy. Anurag Gupta was born and grew up in India, starting his career as a mechanical engineer with Indian Railways for four years. He was the works manager for a workshop built in 1862. They got a grant to modernize the workshop which exposed Gupta to net present value (NPV) and internal rate of return (IRR) analysis, leading him to pursue an MBA at Tulane University in New Orleans. This led Gupta to work for TXU Energy in project finance. TXU had a nuclear plant, Comanche Peak, which was Gupta’s first exposure to nuclear dealing with fuel purchasing and fuel supply. The complexity of nuclear blew him away. The technology and financing of nuclear is physically complex. Every nuclear project is unique and the risk profile for nuclear is not well understood. The amount of capital investment required for a single nuclear plant dwarfs any other energy infrastructure. Once the plant is up and running, nuclear plants are a source of clean power for decades and the variable cost is low. The key risk in nuclear power is safety; the industry cannot afford to have a safety incident. The biggest financial risk is in the construction phase. If a plant can be built on time and on budget, the levelized cost of electricity from a nuclear plant is very competitive. Anurag Gupta has not worked as an engineer in the energy industry, but has always had a finance and project development focus and used his engineering background to translate between the technical requirements and the financial requirements of a project. Anurga Gupta also worked for Ontario Power Generation.
2 - Risk Profile of Nuclear Reactors
Bret Kugelmass: What are some of the types of financing projects that would come across your desk?
Anurag Gupta: Anurag Gupta saw a mix of projects in the nuclear industry, including fuel supply arrangements for TXU’s nuclear plant and structuring the financing around those contracts. The more challenging and interesting work Gupta saw was when he moved into the consulting arena at KPMG. He was lead negotiator and led the KPMG team to advise the U.K. government on its negotiations with Hinkley Point C. Nuclear plants are extremely expensive and take a long time to build, but once they are up and running, the risk profile is decreased compared to the construction phase. Since there is so much money spent up front, the developer must be absolutely certain that the amount of electricity produced over the next fifty to sixty years will be sold at a price that gives an adequate return on the massive up front investment. In the new world order where the electricity markets are liberalized and wholesale prices are set by gas plants, electricity prices have become very volatile. This brings a big amount of revenue risk to the developer. Markets are constructs and reflect a certain policy objective. The way liberalized energy markets are constructed send market signals which don’t support the investment case for nuclear due to large up front capital requirement with recovery over a very long period of time. Markets have not been set up to send accurate price signals for a long period of time.
3 - Role of Government in Nuclear Development
Bret Kugelmass: Will it take government money in order to make nuclear projects come to fruition?
Anurag Gupta: In every single nuclear project around the world, the hand of government shows up in one way or the other. For nuclear programs to take hold and be successful in a country, the host government must have a very active role. Sometimes countries view nuclear as being energy policy, but it is as much industrial policy because it is creating a very complex project which lasts a long time and creates a massive number of long lasting, highly skilled jobs. If a country wants to embark on a nuclear project, it should look at how to harness the meta benefits the country gets in terms of human resources. Ontario Power Generation operates a number of nuclear plants and has a large pool of highly educated, highly trained workers along the supply chain and all of Ontario and Canada benefits from it. Governments can provide a lot of support in making sure supply chains exist and they are taking the right steps to upskill and reskill the workforce. Anurag Gupta used to work for KPMG Canada and moved to the U.K. in 2011 to lead the team on the Electricity Market Reform project. Canada has a long and successful civil nuclear program. Canada’s energy system is one of the cleanest in the world, using a lot of hydro and nuclear. The nuclear industry has a history of cost overruns and schedule delays, which have added to the financial cost and tarnished the reputation of nuclear with the public. Large reactors are assembled on-site in the form of a massive construction project. The question is whether nuclear can move to a model in which a reactor is assembled in a manufacturing setting where costs and quality can be controlled.
4 - Economics of Small Modular Reactors
Bret Kugelmass: If manufacturing efficiencies were brought to the nuclear sector, could costs of a nuclear plant be decreased by tenfold?
Anurag Gupta: A widely accepted definition of a small modular reactor (SMR) is that it is sized below 300 MW capacity. Smaller reactors require less upfront capital to build and, if they are small enough, can be manufactured in a factory environment, transported, and assembled on-site. This allows export markets to open up and remote communities, which don’t need 1,000 MW reactor, open up as markets. SMR’s can also produce process steam and heat. Some of the SMR concepts on the table now have been around for a long time, but their implementation has to do with the economies of scale. Whether you have a 100 MW reactor or a 1,000 MW reactor, the regulatory and safety costs imposed are roughly the same because it’s the same regulatory regime. The more megawatts you can produce to offset the set cost of safety and regulations, the more economic the project becomes. Until very recently, the model has been large industrial scale plants, large transmission lines, and large load centers. That model is under threat and is changing. The SMR community has to look at export markets to spread fixed costs over a large base. At the moment, most SMR’s are in the concept stage or in very primitive design stage; there is no commercially available SMR. In some ways, the risk of SMR’s may be higher because the first unit may not work as planned and there was a large amount of money invested in building a factory. A model in which government takes projects through construction but then benefits from the upsides post-construction has been successful. The Canada InfoBank is a federal institution being mandated to try and bring revenue-bringing infrastructure projects to fruition. Government can support nuclear by writing a check, but also by providing loan guarantees and infrastructure bank programs.
5 - Incentives for Financiers in the Nuclear Industry
Bret Kugelmass: What do you think would be some of the high value actions a government could take right now to kickstart the growth in a small modular reactor industry?
Anurag Gupta: Small modular reactors (SMR) are in a conceptual design phase in most cases. In order to make an SMR program successful, governments will have to make a choice between one or two technologies. Governments can also provide a buyer, such as a power purchase agreement or a utility. There is a tremendous amount of development dollars required to commercialize SMR designs and it will have to be a consortium approach. The concept of project financing is limited recourse, meaning the revenue itself supports the repayment of debt. For that to happen, financiers have to be comfortable with the risk profile of construction and development of nuclear plants. An attraction of the SMR program is, if you can get the first of a kind risk off the table and demonstrate they can be built on a budget in a factory setting, it becomes imminently financeable. In the large reactor market, people talk about first-of-a-kind risk. Because every site is so different, The world absolutely needs renewable energy, such as solar and wind, to combat climate change. Certain jurisdictions are making a mistake by turning its back on nuclear, as it will be a massive source of clean, green, low-carbon renewable power. Nuclear can provide on-demand power if it is required. Nuclear has a big role to play in mitigating climate change by having shown a history of projects that were delivered on-time and on-budget. SMR’s are a reality, not just a concept.
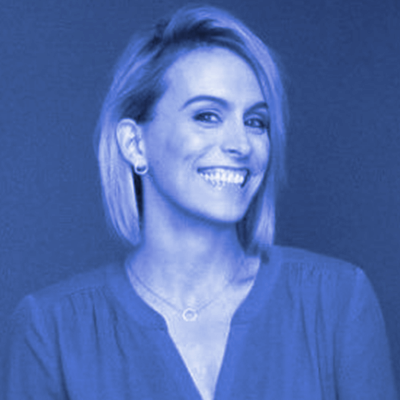
1) Amy’s background in journalism and her personal journey in the nuclear industry reporting on energy from the Wall Street Journal to Axios
2) How energy plays a role in economics and politics including the natural gas boom during the Obama era
3) Nuclear’s environmental benefits and the ways in which it can aid our carbon solution and work against climate change
4) The importance of the US’s leadership role in guiding the global nuclear sector
1 - Intro to Energy Journalism
Bret Kugelmass: How did you get started in journalism to begin with?
Amy Harder: Amy Harder has always wanted to be a journalist and received her undergraduate degree in journalism from Western Washington University. She grew up in Eastern Washington, where the Hanford Site is also located. Harder was driven to the field fundamentally by piecing together multiple layers and is able to do that at Axios. The energy, climate, and environment space is very multi-faceted. Amy Harder started out at the Bellingham Herald, moved to D.C. for an internship, and got a job at the National Journal. She got into energy shortly thereafter, first by starting online discussion boards at the Journal which led her to unveil different battles in geopolitical concerns, along with economics and environmental. Energy is important and undercovered in the media. The energy prices went through the roof in 2008, but now the prices are low and energy issues are currently not a top-tier concern for most Americans.
2 - Energy and the U.S. Economy
Bret Kugelmass: Is everything in the U.S. economy energy-related?
Amy Harder: Energy is tied into everything in the U.S. economy, but largely through indirect ways. Energy is a more pronounced concern when there is the idea of scarcity. A decade ago, the U.S. was building natural gas import terminals and now those terminals are being retrofitted to export natural gas. People track prices of oil every cent it moves because it has such an impact. There should be more attention paid to electricity prices, as the U.S. currently has the lowest electricity prices in a decade. Amy Harder was at the National Journal for six years when she got an offer to work for the Wall Street Journal. She likes to find the subtler shifts in politics, economics, and environmental issues that may not be getting top tier attention.
3 - How Changes in Administration Affect Energy Policy
Bret Kugelmass: During your time working on energy at the Wall Street Journal, what things changed throughout the world at that time?
Amy Harder: Amy Harder worked for the Wall Street Journal from 2014 to 2017. During this time, President Obama shifted left in his policies on the natural environment. In his first few years as President, he talked about the natural gas boom, eventually getting rid of that rhetoric and shifted to more aggressive regulations. President Trump and the scandal that the former EPA administrator Scott Pruitt created has brought more attention to the issues. Since Amy Harder transitioned to Axios from the Wall Street Journal, including a new President and views on climate change. While at the Journal, Harder’s job was to cover the incredibly aggressive regulatory agenda of Obama’s EPA. This has caused Republicans to feel like they must swing the pendulum back to the right. The Clean Power Plan was Obama’s regulation cutting carbon emissions from power plants. The U.S. Supreme Court stayed the regulation in February 2016, which was an unprecedented move, but there were significant legal questions about the regulation. Amy Harder first reported on nuclear during her time at the National Journal, but she did have one nuclear story at the Wall Street Journal that struck a chord. Her story was about environmentalists softening opposition to existing nuclear power plants and received the most backlash of any story she wrote while at the Journal. Nuclear power is the most controversial energy source, just ahead of fracking. After attending the U.N. Climate Change conference in Germany last year, Harder wrote a column about the left’s nuclear problems. She spoke with five Democratic Senators individually while at the conference, who all showed varying levels of support with caveats. A lot of Democratic politicians are very vague have a hard time saying outright what their position is, whether that is in support or opposition. The same goes for politicians on the right who support nuclear power, but say they don’t care about climate change.
4 - Controversy and Divisiveness of Nuclear Power
Bret Kugelmass: Is there a way to shift the conversation of nuclear to allow some environmentalists with the potential of nuclear technology?
Amy Harder: There is a cultural feeling that runs through a generation of people who grew up in the 1960’s who have a fear of nuclear power. After Chernobyl, Three Mile Island, and Fukushima, people had real fear. Germany stopped all nuclear power after Fukushima. Some people want to stand behind the problems as a reason not to support nuclear or see its potential. Concern about climate change is genuine, but there is a cognitive dissonance going on. James Hansen, a very well known climate scientist, and Bill McKibben, founder of 350.org, a heavily influential activist and environmental group, have had tension about McKibben’s position on nuclear power. McKibben’s official position now is that he doesn’t have an official position on nuclear power. Across the political spectrum, the more controversial and divisive a topic is, the less likely an official position will be taken by the groups that matter most.
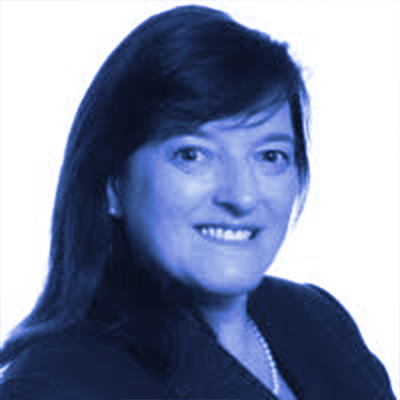
1) Tina’s background in chemical engineering and her personal evolution in the nuclear industry and early work at Northeast Utilities
2) Comparing the overall environmental impact and health risk across different energy sources including nuclear
3) Risk-based versus prescriptive approaches to licensing new designs in the US
4) Key drivers of research in plant modernization including technology to automatically monitor chemistry
1 - Path to Nuclear Through Chemical Engineering
Bret Kugelmass: How did you find yourself in an engineering field?
Tina Taylor: Tina Taylor studied art in high school and wound up in a chemistry class, where she performed well and found that she loved the subject. Her teacher advised that she explore chemical engineering for college and ended up getting a degree in that field from Tufts University. After graduation, Taylor hired on with Northeast Utilities working in nuclear power. Northeast Utilities, headquartered in Connecticut, had the Connecticut Yankee plant and three units at Millstone, also providing services for the Seabrook plant. Taylor worked at headquarters focusing on chemistry, materials, and corrosion. One issue the utility was experiencing was pitting of steam generator tubing. Sludge was building up on the tube sheet and around the tubes, allowing chemicals to concentrate very close to the surface of the tubing, causing an aggressive chemical solution to exist which would chemically corrode the steam generator tubes. Chemical control can be used to prevent this corrosion, as well as cleaning with the use of a water lance. The Electric Power Research Institute (EPRI) is a repository for the nuclear industry in terms of data, reports, and people with different backgrounds.
2 - Materials Management in Nuclear
Bret Kugelmass: What does B&W Nuclear do?
Tina Taylor: Tina Taylor worked at B&W Nuclear before joining the Electric Power Research Institute (EPRI). B&W mainly worked to support the fleet of B&W once through steam generator plants. During her time at B&W, Taylor worked on development of an electrochemical monitor to monitor the electrochemical potential (ECP) in the feed water. ECP tells the oxidation potential of the water in combination with a metal. In nuclear, an issue such as degradation arises at one plant and the industry examines whether it is design or plant specific or whether it is potentially generic. Around 2000, the nuclear industry formed a more proactive approach to materials management and EPRI worked to develop a roadmap of everything that might happen, called the Materials Management Matrix. Research was put in place to better understand if or when different phenomena would occur, how to inspect for those phenomena and at what timeframes to inspect. When Taylor worked at Northeast Utilities, she was a member of EPRI and worked on several research projects, continuing to work with EPRI during her time at B&W as well. She took a job at EPRI when an opening came up in the chemistry area, working on computer codes that predict and calculate high temperature chemistry. An area that’s boiling concentrates chemicals in the feed water, so in areas of high heat transfer there can be locally strong solutions. In the turbine, wet steam goes through the turbine and creates condensation, also creating concentrated solutions. Tina Taylor worked in the chemistry department to develop a sophisticated tool called SMART chem WORKS which collected data from power plants and analyzed that data against the limits or to look for trends. There was also the implementation of fingerprinting, an early approach to artificial intelligence which matched data from the plant with model results that could cause anomalies in the plant and offered this as a service to industry. Taylor then moved to EPRI’s new subsidiary, EPRI Solutions, which aimed at helping to provide more services associated with their research.
3 - Tradeoffs of Different Energy Sources
Bret Kugelmass: Is EPRI, a non-profit, allowed to spinoff for-profit entities?
Tina Taylor: It is important that the Electric Power Research Institute (EPRI) segregates the work done into taxable and non-taxable work. When EPRI Solutions were formed, many people were brought over from the existing EPRI staff and the director, Tina Taylor, enjoyed the entrepreneurial environment. While she was there, Taylor also started managing a larger software team and took on an environment group within EPRI. Eventually, EPRI Solutions folded back into EPRI. The work EPRI does related to the environment spans all aspects of generating electricity, transmission, and end use across all energy sources. One focus was life cycle impact, which looked at the tradeoffs between tradeoffs that use a lot of land, water, or have a waste stream to compare different technologies. It’s important to put the impact in the context of the group, organization, or society that is looking at what energy technology to implement. To determine the best thing to do going forward, there needs to be a common currency, such as the dollar or carbon, to determine the value of using land or water. After eight years in the environment group, Tina Taylor returned to the nuclear group post-Fukushima. EPRI has grown in the nuclear field into multiple international engagements. The regulatory drivers and the need for nuclear energy vary in different countries, creating different cultures and priorities around nuclear. The U.S. has a lot of flexibility to use risk-based approaches to prioritize work.
4 - Modernization in Nuclear Power Plants
Bret Kugelmass: What are some of the key drivers of research in the area of modernization?
Tina Taylor: The Electric Power Research Institute (EPRI) has always looked at how new technologies can be used beneficially in power plants. Over the past five to ten years, there has been a big focus on sensors and using data. EPRI pulled together work across multiple technical areas to think about how sensors can go beyond monitoring equipment or inform maintenance needed and be used to understand radiation fields in parts of the plant and monitor the chemistry in plants. EPRI’s project called Value-Based Maintenance looks at using the knowledge in the data collected by all the plants and determining a cost-optimized approach to reliability. The industry is trying to focus on the right reliability at the right cost by looking at tradeoffs between proactive and reactive maintenance. Information in models and operating experience is used to understand how the equipment in the nuclear plant is related to safety, allowing focus on components that more directly impact safety.
5 - EPRI U
Bret Kugelmass: Are there elements of safety that could be reanalyzed to see if they are necessary or have adverse effects?
Tina Taylor: The nuclear industry takes personnel safety, as well as plant safety, very seriously and no one is suggesting backing off in that category. The Electric Power Research Institute (EPRI) recently launched a program called EPRI U. Tina Taylor and her team took a hard look at the work EPRI has done over the years on training, workforce development, and qualification of workers and wanted to be more deliberate about helping to train more people and giving utilities tools to more efficiently train their workforce. EPRI is taking their knowledge products and making them more widely available through distance learning via online resources. One compelling technology element across the whole energy industry is the use of virtual reality and augmented reality. Augmented reality could be used with Google Glasses to look at a pump and pull up information about its maintenance history. One project looks at how to use augmented reality and virtual reality in training spaces. EPRI created a 3D model and linked it with a procedure to take it apart, maintain it, and put it back together. This tool allows someone to take a walk through a component, for example, if engineers want familiarly with the component, but can also be used to train and test maintenance personnel to perform work on the equipment.
6 - Augmented Reality in the Nuclear Industry
Bret Kugelmass: How is augmented reality and virtual reality valuable in the nuclear sector?
Tina Taylor: At nuclear plants, getting someone proficient and prepared for a nuclear environment is valuable. There is also value in getting a lot of people familiar with what goes on inside the plant and what the equipment looks like without physically going in the plant. Making it inexpensive and easy for people to have experience with different equipment in the plant can add a lot of value. There is real potential for bringing information with you have having information at your fingertips while you’re in the plant environment. It has gotten very inexpensive to do a 360 video of a power plant space and it is now a common part of the pre-job brief. These videos can point out radiation fields and specific pieces of equipment. Tina Taylor has seen the industry move from problem solving to looking for opportunities. She is inspired by the emergence of the advanced reactor ecosystem that exists. Existing plants in the U.S. are extending their life, but there are a lot of new technologies coming along to keep innovating and doing things better.
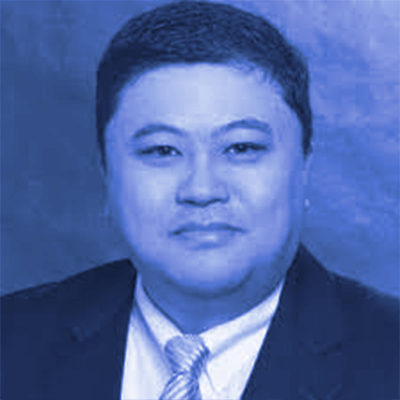
1) Aladar’s background in material science and his personal journey in the nuclear industry from the NRC to EPRI
2) Ways in which the NRC regulates civilian use of nuclear materials and its role at Yucca Mountain
3) EPRI’s research improving fuel rod coating to slow down oxidation and prolong fuel cycle within a pressurized water reactor
4) Ways in which EPRI is working to accelerate the deployment of these concepts
1 - Path to Nuclear through Material Science
Bret Kugelmass: Where did you get started?
Aladar Csontos: Aladar Csontos studied material science at Johns Hopkins, specifically working on tank armor and tank material for his thesis. Tank material is magnetic and its properties can be changed and manipulated to look like it has a magnetic signature of a car. This was primarily a big issue in the late 1980’s and early 1990’s in Eastern Europe, because the mines would go after only tanks based on the magnetic signature. Aladar Csontos developed microscopy skills during this process and also during grad school at UVA. During grad school, Csontos also worked for Ethyl Petroleum Company and showed in the microscopy how nanoparticles of carbon were causing corrosion on diesel engine parts. If the agglomeration of the nanocarbon subparticles could be removed, the engine would be much longer lived. When Csontos went to the Electric Power Research Institute (EPRI), he learned about what it took in terms of the infrastructure cost, supply chain issues, and changes that come with innovation of a new material. Csontos spent 15 years at the Nuclear Regulatory Commission (NRC) before going to EPRI, spending some time at Yucca Mountain, transportation, and dry storage. Right after grad school, Csontos worked at the Center for Naval Analysis working out logistics issues related to Operation Enduring Freedom after 9/11. During this analysis, he realized that nuclear carriers didn’t need anything other than the jet gas for the airplanes, getting him thinking about how much gas money was saved. This peaked Csontos’ interest in nuclear and Yucca Mountain had a great public service aspect to it, looking at how to store and dispose of waste safely. Csontos started working on canisters and the engineered barrier system at Yucca Mountain.
2 - Degradation Phenomena at Yucca Mountain
Bret Kugelmass: What are the engineered barriers at the Yucca Mountain site?
Aladar Csontos: Some engineered barriers at the Yucca Mountain site include the nickel alloy for the canisters and a drip shield. The Nuclear Regulatory Commission (NRC) has the role and responsibility to regulate the civilian uses of nuclear materials. The Department of Energy (DOE) is responsible for licensing the repository. Al Csontos worked on the regulatory side of ensuring the repository at Yucca Mountain would safely operate. While at Yucca Mountain, Csontos also looked at the safety of piping with degradation and how to manage degradation. He worked closely with folks from the Electric Power Research Institute (EPRI) who were evaluating different degradation phenomena, such as stress corrosion cracking, pitting, and crevice corrosion. This was a large area of research called the Materials Initiative that occurred over a 15 year period. Stress corrosion cracking is a combination of electrochemical corrosion plus stresses that allow a crack to grow. The combination of stress corrosion cracking and pitting in canisters for dry storage was a concern and the degradation mechanisms had to be managed, such as chlorides on stainless steel. Salt has caused pitting and cracking on nuclear sites, as well. EPRI is working on how to inspect pits and cracks and how to mitigate against pitting. Management of long term storage of the dry cask storage systems has been a global problem. When two materials are in contact with each other and there is a layer of water in between and dissimilar metals, dissimilar corrosion of one kind or another can result.
3 - Accident Tolerant Fuel Development
Bret Kugelmas: Is there a focus on alloy development because new alloys have properties to resist phenomena that has been observed over time?
Aladar Csontos: Sometimes new alloys are developed; many locations that have alloy 600 reactor pressure vessel heads have moved to alloy 690 due to stress fracture cracking. Other areas don’t make material changes, but instead mitigate and repair. Spray technologies for coating surfaces with new metals is being looked at for stainless steel canisters. Cracking issues may be able to be mitigated by laser peening, which imparts a compressive residual stress on the surface of the canister. Al Csontos sees that many safety benefits are tied to economic benefits, such as the benefits of dry storage aging management. Al Csontos left the Nuclear Regulatory Commission (NRC) at a time in which he was concerned about the future of nuclear. An opportunity to work at the Electric Power Research Institute (EPRI) in the area of accident tolerant fuels and Csontos was highly interested in pursuing the subject due to his desire for public service and the recent Fukushima incident. Accident tolerant fuels are fuel concepts that will reduce the probability or coping times from an event like Fukushima or a meltdown. If fuels could be more resilient and robust, there is more time to address an emergency situation. EPRI has done more analysis of other types of design basis accidents and anticipated operational occurrences, which are scenarios that the NRC requires vendors to look at for their fuel capabilities. Accident tolerant fuels are now called advanced technology fuels (ATF). ATF’s provide an extra one to three hours of benefits. One concept is coated cladding. A normal zirconium fuel is coated with chromium, which is more resistant to failure and can operate at higher temperatures.
4 - Economic Benefits of Minimizing Oxidation
Bret Kugelmass: What temperature does oxidation start at?
Aladar Csontos: Oxidation occurs all the time, including rust and corrosion. Rapid runaway oxidation occurs at a much higher temperature. By putting a chromium coating on the zirconium, it doesn’t oxidize as fast and at higher temperatures. If the fuel can be left in the reactor longer, there are economic benefits. If the enrichment and burnup can be slightly raised, the intervals can be extended to two years and another cycle can be added in the fuel life. One study the Electric Power Research Institute (EPRI) completed in 2005 showed that there are benefits to going to two year intervals and the industry is interested in going towards this goal. Chromium oxide is very hard and, based on current observation, acts like a very good protector against debris damage. Right now, the Nuclear Regulatory Commission (NRC) has approved the underlying layer, the zirconium fuel rod bundle. Putting an additional layer increases safety, not decrease, but there is still a question about delamination. Hatch Southern Nuclear has placed in two types of advanced technology fuel (ATF) concepts. One is an oxide coating, a ceramic armor coating. Small segments of fuel rods have been placed into Hatch to see how it reacts and how it operates during normal operations. A ferritic steel, iron chrome aluminum alloy, was also placed inside to see how it would respond under normal conditions.
5 - Advanced Materials in Advanced Technology Fuels
Bret Kugelmass: Are there other types of approaches in advanced technology fuels (ATF)?
Aladar Csontos: Some advanced technology fuels (ATF) focus only on the cladding. Inside a fuel rod, there is a stack of uranium dioxide fuel pellets inside a zirconium rod. This zirconium alloy has been optimized over the past 35 years and fuel vendors have created a very good fuel. The Electric Power Research Institute (EPRI) is looking into how fuels can be made more cost effective in terms of efficiency and cost benefit analysis. The Department of Energy (DOE) funded the development of these concepts after Fukushima and has focused on three different concepts: coatings, ferritic steel, and a silicon carbide concept with a different fuel pellet, a uranium silicide fuel that has more uranium atoms, which allows for more power. Another concept, Lightbridge, is a metallic fuel that has a twisted cruciform shape, which increases conductivity. The focus of Lightbridge is on the current fleet, but also in the next generation of reactors. EPRI is looking at how to bring technologies to market faster. The traditional fuel development time has been 20+ years. The Nuclear Regulatory Commission (NRC) needs to know what the product will be able to withstand for a safety argument to the public. A lot of tests need to be performed across many different parameters and in different conditions, including irradiation of materials and post-irradiation exams. There may be ways to collect data in-line or while it’s being tested or operated to make sure no limits are encroached on. Advanced sensors and advanced non-destructive examinations interrogate the fuel assemblies and fuel rods to make sure they are operating safely. There needs to be more regulatory certainty or understanding of longer term concepts that have greater value.
6 - Nuclear Fuel Development Process
Bret Kugelmass: What is the shortest period of time to go from concept to implementation of new fuel utilizing new techniques?
Aladar Csontos: Using new techniques, a new fuel could go from concept to implementation in less than ten years. There may be ways to do advanced modeling ahead of time to get at some of the materials issues beforehand to predict how the material will behave, so research and development should focus on advanced modeling. With advanced non-destructive evaluation (NDE) and advanced sensors, a predictive framework can come together to provide health monitoring of the fuel. Development of the coatings itself can be done in a very short timeframe. There are a lot of test reactors internationally and domestically. The Department of Energy (DOE) has the advanced test reactor (ATR) at the TREAT facility. Accelerated testing aims to show how materials and properties change over time. This data can be used to predict how the fuel will perform long term for the different cycles. A lot has been learned from reactor operations over the past 60 to 80 years. The Electric Power Research Institute (EPRI) has a big role in certain areas like water chemistry, since they create the guidelines. The fuel development process is iterative and sequential. Going from fuel lead test rods (LTR’s) to assemblies to a couple of assemblies to a batch of assemblies in sequence increases the level of confidence. Aladar Csontos is optimistic about advanced fuels. Nuclear is cost effective because of the low cost of fuel. There is an opportunity to increase the efficiency on the cost side of the fuels even more, in fuel cycle optimization. In the future, coated fuel rods will bring safety, more enrichment and burnup will bring efficiency, and longer cycle times will allow power to be generated for longer periods of time. Resilient fuels may be able to work better with solar, wind, and hydro, which could be a long term benefit to the U.S. energy portfolio.
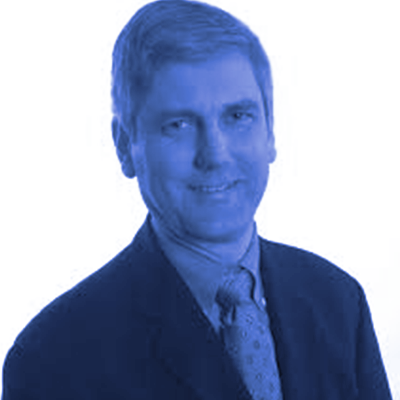
1) Andrew’s background in physics and optics and his personal journey in the nuclear industry
2) An understanding of the metal wastes like uranium in weapons facilities and their effect on the environment
3) Chernobyl and how the facility was salvaged after the accident
4) EPRI’s recent study on factors that control nuclear destiny including economics and policy
1 - Uranium Chemistry in the Environment
Bret Kugelmass: How did you get into the nuclear space?
Andrew Sowder: Andrew Sowder studied physics, specifically optics, at the University of Rochester. After graduation, Sowder went to North Carolina State University for a fellowship in nuclear engineering and then went to Clemson to major in environmental health physics, completing his PhD on uranium chemistry in the environment. Sowder completed some post-doctoral research focused on cleanup of the nuclear weapons complex at the Savannah River Site. Most of the uranium Sowder looked at was a co-contaminant with other heavy metals that were discharged in the riparian wetlands environment using the contemporary practices of the day. The team looked at how metals went up the food chain and nickel turned out to be the bigger hazard. Uranium liked to form very strong associations with the soil and organics in the soil, so it was tightly bound in the sediments. Nickel tended to be more mobile and available to travel up the food chain. The biggest problem from uranium was radon, which is part of the decay chain. Radon is a noble gas that can be transported and inhaled into lungs, where it decays into things that stick to the lung tissue which causes the most damage. Uranium tends to be more of a chemical toxin than a radio toxin, acting more like a heavy metal. Popular media tends to confuse the idea of the presence of radioactivity with an unbounded risk.
2 - Domestic and International Nuclear Outreach
Bret Kugelmass: How did you transition into the State Department as a foreign affairs officer?
Andrew Sowder: The American Association for the Advancement of Science administers science policy technology fellowships. This fellowship brings scientists and engineers into the policy environment in D.C. to provide technical inputs. Andrew Sowder’s fellowship was at the Environmental Protection Agency (EPA) in the Office of Radiation and Indoor Air, which was working on an outreach project with the Navajo nation dealing with abandoned uranium mines and contaminated well water. There was real potential for exposures in this community because people had incorporated mine tailings and uranium ore into the concrete in walls and structures. Sowder brought radon detection equipment and other instruments to the community and completed testing. Andrew Sowder was hired into the State Department to complete oversight of U.S. assistance to the Chernobyl shelter program. Unit 4 was the reactor involved in the Chernobyl accident; one or two of the other units continued to operate after the accident, as they were unharmed during the explosion and Ukraine needed reliable electricity during the winter. At least one of the reactors also had to stay operational to provide heat to the nuclear site; a coal plant was later sponsored by the U.S. to be built on-site to provide district heating. Chernobyl. U.S. led in raising funding for Ukraine to manage the reactor issues and other funds were raised for management of spent fuel. Sowder transitioned to the Electric Power Research Institute (EPRI) as his family started growing and they moved to Charlotte, NC.
3 - Nuclear Fuel Cycle
Bret Kugelmass: What were some of the initial things you worked on while at the Electric Power Research Institute (EPRI)?
Andrew Sowder: Andrew Sowder has been tied to the nuclear fuel cycle at EPRI, but came in working on a program for Yucca Mountain. EPRI was the only other program, besides the U.S. Department of Energy (DOE), that was developing and conducting assessments on total system performance of the repository. EPRI’s U.S. members were paying into the nuclear waste fund and had an interest in the repository. There is no such thing as a perfect site; the goal should be to have an adequately safe site that meets the regulations and protects the public. EPRI exited from Yucca Mountain a year before the termination of the project, but they did review a history of where they ended up with regulations and recommendations for future evaluation of repositories. Both the Environmental Protection Agency (EPA) and the Nuclear Regulatory Commission (NRC) rolled out new rules, regulations, and standards for repositories and had jurisdiction. EPRI can weigh in with technical insights without advocating for a position. There are different repository approaches around the world, including levels of compliance for storage. The term “accident tolerant fuels” came out of post-Fukushima events and the desire was to have a nuclear fuel that could delay or prevent another core meltdown like happened at Fukushima. Development of these fuels were already in place, but were focused on robustness instead of coping time for operators. The biggest drawback to zirconium cladding is the higher temperatures in the presence of oxygen and water, which creates runaway oxidation reactions that lead to further generation of heat. During a shutdown in a standard, traditional reactor, the heat must be removed because it keeps building and something will fail. The general concept is to improve the cladding with a coating or substituting it with a different material that doesn’t have the same drawbacks as zirconium.
4 - Advanced Materials in Nuclear Fuels
Bret Kugelmass: What other materials don’t oxidize with higher temperatures like zirconium does?
Andrew Sowder: There is no such thing as a meltproof or accident proof fuel in a light water reactor system, because at a certain temperature, all materials will fail if heat is not removed. The original reactor fuels in the U.S. were stainless, but they imposed a penalty because they absorbed neutrons. Another equivalent that was proposed was an Iron Chrome Aluminum (FeCrAl) alloy that was an analog to the stainless steels of the past. The more advanced approaches move away from metallics and towards things known to withstand high temperatures, such as silicon carbide. Like zirconium, they don’t absorb many neutrons, but it is brittle and is more difficult to work with. If more coping time can be demonstrated, then the plant may be less reliant on a certain safety system and typically, lowering the classification of systems is less expensive to maintain. Eliminating or reducing the dependency on certain systems comes with savings. Even though fuel is a relatively small fraction of the cost of a nuclear plant, it is still important and there is a focus on longer cycle lengths and more performance because it contributes to the economic performance.
5 - Benefits of Advanced Nuclear Concepts
Bret Kugelmass: Tell me about some of your work in understanding and communicating the issues around advanced reactors.
Andrew Sowder: There are a number of developers and entrepreneurs trying to develop the next big concept in nuclear. The value and benefit of nuclear is that it is unique in what it provides in one package: scalable, dispatchable, energy dense, and the focus on limiting emissions of greenhouse gases and other environmental factors. Should storage come into fruition at a sufficient scale, renewable can start filling those same niches. If carbon capture sequestration gets developed to a point at which it is economic at scale, then natural gas can perform in that niche. While the current nuclear fleet is operating safely, new nuclear designs offer the promise of simplification, greater margins, reduced emergency planning requirements, and reduced staffing costs. With lower pressures come lower pressures come thinner wall components and maybe lower costs. Most advanced concepts operate at a substantially higher temperature, which brings a higher efficiency electricity generation. This heat can also be used to produce chemicals and hydrogen. The Electric Power Research Institute (EPRI) receives many requests from the developer community for help understanding what customers want. Developers must consider what the market will be like in five or ten years and what the customers will want. The customer is the owner/operator, not just utilities. Some of the greatest gains in new markets will not be solely for electricity.
6 - Nuclear Heat Production
Bret Kugelmass: Are your economics three times better in nuclear heat production?
Andrew Sowder: There is a benefit of not converting from one form of energy to another and maybe having to convert back again. Electricity is very transportable and can be accessed where it is needed once it is on the grid. What you gain in efficiency in heat production, you lose in flexibility. There have been proposals of energy parks, where a reactor is sited and industrial development is encouraged around it. The Electric Power Research Institute (EPRI) and the Idaho National Lab (INL) are looking into hybrid energy systems. EPRI has a model called Regen which models what expansion of which generation assets or mixes are needed to meet certain criteria. If the plants costs less to build and operate, it encourages the model to say nuclear has a promising future. Favorable policy related to carbon constraint or cost also drove nuclear builds according to the model. Another factor in the success of nuclear was revenue. If the nuclear owner/operate received extra revenue, the level of revenue had the greatest impact on the model. EPRI is looking into the real value of a nuclear plant and other technologies. Understanding what value different assets bring and what you lose when you remove them from the system is on the cutting edge of where people are today in understanding how markets are priced.
7 - Measuring Value of a Power Plant
Bret Kugelmass: What are all the characteristics of value of a power plant?
Andrew Sowder: Some markets may receive some values that others may not. Because the electricity grid was built using coal and other plants that had big spinning turbines and generators, there ended up being a lot of inertia on a system and frequency regulations. Wind can produce something that is a synthetic version of that and introducing storage helps as well. Black start capability is in conversation for advanced reactors. When the grid becomes unstable, nuclear plants currently need to shut down. There are applications for nuclear where it doesn’t need to be connected to a grid in a microgrid operation. During the 2014 polar vortex, the U.S. had a curtailment or loss of natural gas supplies to electric power production because home heating is given preference, creating a reduction in gas pressure. There were also coal piles that froze in the South. Having a plant that doesn’t need fuel brought to it and could ride out the storm has strategic value. There is a big opportunity in the U.S. and the world where there is an interest in bringing old concepts back to light. Depending on what you believe to be problems and challenges of the future, whether it be climate change, energy supply, resource limitations, or others, there is a need or value to having an option like nuclear that could step in and be deployed if needed. The real benefit value of nuclear and continuing to invest in nuclear energy is that it provides you with a valuable option for the future that is available if you need it. In the financial market, options have real tangible value and options should be kept on the table.
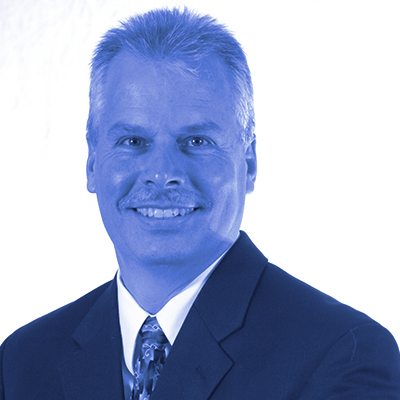
1) Dave’s background in welding and his personal journey in the nuclear industry
2) Fatigue and creep in fossil plants
3) The use of 3D printing in additive manufacturing on an industrial scale
4) Improving the time and cost of producing small modular reactors and Gen IV reactors
1 - Metallurgy and Nuclear
Bret Kugelmass: How did you get started in the nuclear space?
Dave Gandy: Dave Gandy’s background is in metallurgy, which he studied at North Carolina State University, leading him to start out in the welding area. He moved over to work for the Electric Power Research Institute (EPRI) in 1996. Dave Gandy had done an internship with J.A. Jones Applied Research working in the welding area, mostly focused on manual stick welding or semi-automatic gas tungsten arc welding to support pipe replacement in the boiling water reactor. In general, most piping in nuclear plants have welded joints. Quality inspections are performed on welds with non-destructive evaluation (NDE) tests, usually ultrasonic, which can detect anomalies or manufacturing defects. Inspections are completed before startup and at set intervals throughout the life of the plant. When Dave Gandy started with EPRI, he focused on a lot of fossil related activities, specifically metallurgy in the high temperature area. The team looked at different components to determine material fatigue or failure methods. In a fossil plant, the main concerns are fatigue and creep, due to the exposure of time, temperature, and stress. The alloying elements, such as molybdenum or nickel, give materials the strength and capability to perform as designed. In general, the conservative nuclear industry tends to stay with well-known, well-performing alloys, unless a revolutionary material comes along.
2 - Advanced Manufacturing Techniques
Bret Kugelmass: Is manufacturability an issue when dealing with different alloys?
Dave Gandy: Certain manufacturing tools are used for much stronger alloys and may need to be bent at a different radius or string rate to get it to the final component size and geometry. Typical fossil plants in the U.S. operate around 1050 degrees F. In 2008, Dave Gandy moved into the Electric Power Research Institute’s (EPRI) technology innovation area, which looks into long-term research development. Technologies at the time included nanocoatings for insulators and power line cables, which minimizes ice build up. From a power plant perspective, there will be a few components that are produced with additive manufacturing, also known as 3D printing. Some of these components could be reactor internals, small valves or pumps, or replacements for obsolete components. When a part goes through additive manufacturing, it typically goes through a solution anneal at a high temperature with water coolant or a hot isostatic press. Tensile properties are generally quite good, but toughness tends to lack in this process. This could be due to impurities in the atomization process. EPRI is working on putting together a two-thirds scale small modular reactor (SMR) and is making very large girth welds with electron beam welding. Electron beam welding can be done in a single pass and does not require any filler material, and there may be no visible evidence of the weld after it goes through a final heat treatment.
3 - Electron Beam Welding
Bret Kugelmass: What are the advantages of electron beam welding’s narrower heat affected zone?
Dave Gandy: The heat affected zone has different properties from the base material. Alloys go through solution anneal or heat treatment to bring it back to a similar property or microstructure of the base metal. The Electric Power Research Institute (EPRI) believes electron beam welding can eliminate about 90% of the standard welding time on a typical large girth weld. Small modular reactors (SMR) and Gen IV reactors must be made in a different way, by being physically made in a shop environment and then shipped to the plant for installation. Many of today’s large reactors are large forgings made in Japan, Korea, China, and other places and shipped to the U.S. Due to the size of the reactor vessels, the forging process requires a very large forge and a massive ingot. Only a certain number of vendors can make these components. Electron beam welding has been around for about 50 years and typically requires being placed inside a large vacuum chamber. EPRI is looking to build one of these chambers. Dave Gandy has been working on a project in powder metallurgy since 2010, which can be combined with hot isostatic press. Powder is placed inside a can, sealed with a vacuum, and placed in a hot isostatic press, which produces a solid material with the geometry of whatever component you were trying to make. Components that could be manufactured with this process include large valves, pump housings, reactor heads, and steam generator heads. EPRI is working with industry to bring forward a consortium that will help install a large hot isostatic press.
4 - Powder Metallurgy Hot Isostatic Press
Bret Kugelmass: Are there other industries that have expressed interest in advanced manufacturing techniques?
Dave Gundy: The offshore oil industry is ahead of the nuclear industry in terms of advanced manufacturing, specifically powder metallurgy hot isostatic press (HIP). In 2010, the Electric Power Research Institute (EPRI) spent a lot of time getting ASME qualifications in place for this process. Newer nuclear reactor designs are going to operate at higher temperatures than are currently being used. Higher operating temperatures require better ways to manufacture some of these components and some casting and forging technologies may not work for certain applications. There are a number of advanced nuclear plant companies that are starting to look at how specific components are manufactured and how to put their technology in place. The U.S. does not have the infrastructure together today that they had twenty or thirty years ago to perform all the manufacturing, so there must be other ways to assemble the components. EPRI made a number of components early on with 316L stainless steel; during manufacturing, all would have good strength, but some would have poor toughness and some would have good toughness. Strength is the ability to hold a particular structure in place. Toughness is the ability to absorb impact. The 316L powders were producing a variety of different results in toughness based upon how the material was being handled. The team determined that, if they could control the oxygen levels in the powder, they could control the toughness. This control is done during the atomization process.
5 - Additive Manufacturing in Nuclear
Bret Kugelmass: Is there any way to actively rip the oxygen off the outside of the 316L stainless steel particle with some other chemical process?
Dave Gandy: Some vendors are looks at ways to actively rip the oxygen off the outside of the 316L stainless steel particle, but this process does not currently exist. One of the areas the Electric Power Research Institute (EPRI) will be focusing on over the next five years is additive manufacturing. There may not be a large number of power plant components made with this process, but there are certain components to which the technology would lend itself well. There must be good specifications for additive manufacturing that allow nuclear quality components to be made. Only one alloy is being looked at right now, but there are seven or eight alloys used routinely throughout the power industry that must also be developed. Ferritic alloys are more susceptible to oxygen pickup, so they must understand oxygen issues and how to process them. Moving toward advanced generation nuclear components, there will be higher temperature alloys. Nickel-based alloys rely on cobalt to provide some level of strength and capability, but cobalt is not a good actor in a nuclear environment, so new nickel alloys must be developed. When activated, cobalt can become a radiation source. There will be alloy challenges in erosion resistance, oxidation issues, and creep performance. Dave Gandy is a big believer in innovation; the U.S. will rise to the top in advanced generation nuclear.
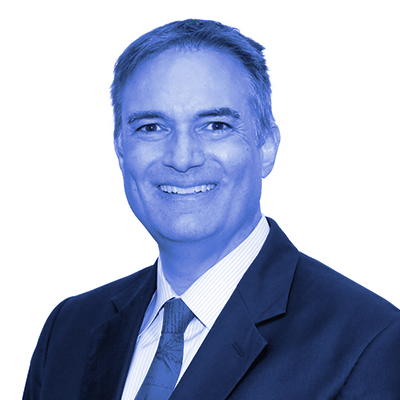
1) Rob’s work in plant modernization managing major electrical and digital upgrades at plants in the US
2) Economic challenges in nuclear and how we can replace manual labor with automation to help overcome those challenges
3) How cybersecurity is maintained in digital systems
4) How plant modernization methods are working to dramatically reduce the operation and maintenance costs required in nuclear
1 - How Three Mile Island Sold Rob Austin on Nuclear
Bret Kugelmass: How did you get into the nuclear industry?
Rob Austin: Rob Austin received a Bachelor’s degree in history from Davidson College, followed by a year in law school at Georgetown. Afterwards, Austin received a degree in engineering from Florida Atlantic University, where he studied acoustics and underwater sound propagation. Rob Austin then went to Electric Boat, the primary submarine designer and contractor for the U.S. Navy. Electric Boat got its start around the Civil War period, built diesel electric boats in World War I and II, and was then chosen by Admiral Rickover to be the constructor for the first nuclear submarine, the USS Nautilus, which was launched in the mid-1950’s. Austin’s role at Electric Boat was working on the design for the Virginia-class attack submarine in mitigating sound from the engine room. His real exposure to nuclear came when he worked for Duke Engineering and Services, a subsidiary of Duke Power, which was acquired by Framatome. Austin was working on the non-nuclear side of energy, but knew Framatome would prioritize nuclear. He started researching Three Mile Island and Chernobyl and walked away with a fascination of the promise of nuclear and how it has been misunderstood by the general public. The partial meltdown at Three Mile Island could have and should have been avoided, but the design of the plant and containment worked and prevented the spread of radiation. The industry looked at Three Mile Island to determine how they could improve and make the technology better since the plant was now non-recoverable. There is a disparity between what happens at these accidents and what the public seems to think happened.
2 - Avoiding Digital Obsolescence in Existing Reactors
Bret Kugelmass: How did you end up pursuing a career in the nuclear space?
Rob Austin: Rob Austin managed major electrical and digital upgrades at nuclear stations across the U.S. while working for Framatome. Most of the plants were built with analog controls and electronics, or very early generation digital. The U.S. plants have invested and adopted digital controls on their non-safety related systems since they are more reliable than analog systems. Most plants have digitally-controlled turbine generator systems and feedwater systems. They have been slow in embracing digital on the safety-related systems, such as reactor protection systems and safeguard systems. International upgrades took place to prevent obsolescence of components and parts that are no longer manufactured or supported. Plants may also consider a digital upgrade because digital controls are traditionally more reliable than analog controls. New digital systems don’t last as long, however, these controllers are rugged and have a longer life than consumer electronics. Plants can handle digital obsolescence by becoming more agile as they upgrade so they are able to adopt newer technology as it becomes available. If digital controllers are expected to last ten years and the plant is licensed for sixty years, spares can be purchased to anticipate equipment replacement.
3 - Digitization in Nuclear Plant Systems
Bret Kugelmass: How can you build something with so much computational power, but also expect it to last 100 years?
Rob Austin: The required complexity of digital controls for nuclear plants must be considered and it must only be as complex as it needs to be. Safety-related systems that measure a reactor and provide a response during an abnormal incident need to be planned ahead for, not the larger IT structure of the plant, such as how drawings are managed or how teams communicate. The overall electrohydraulic design of the plants were designed to be robust and reliable. Flux or neutron measurement provides the state of the core, and coolant flow and temperature provide the thermal output and power of the reactor. Plants have multiple systems for control and protection, which provides a higher plant resiliency. The driver for upgrading to digital may be so some plants can develop an obsolescence strategy and maintain their current systems. A safety-related control system should not be affecting the economic bottom line of the plant, so systems that do affect the bottom line should have a focus on modernization. These include tasks that are currently done by manual labor and automating them. The primary concern for upgrades in the U.S. is how to do it economically. The nuclear industry has a tendency to take items developed in other industries and add on additional requirements or compliance checks, which adds significant cost to the project.
4 - Software Common Cause Failure
Bret Kugelmass: What is software common cause failure?
Rob Austin: Critical nuclear protection systems are redundant, with two or three chains of the same instruments going to the same actuators for the same safety function. The concern with moving the software systems is taking temperature values to a digital device which would examine the temperature using software. If there was a flaw in the software, it would carry across all redundant instruments, which is known as software common cause failure. The Electric Power Research Institute (EPRI) has done a lot of research into the operating experience of systems that are installed, as well as the risk impacts. One or two edge cases had software common cause failure, but the conclusion was that the existing methods of qualifying and developing software is good enough to ensure that this doesn’t occur. If it does occur, normally a plant will rely upon operators to take notice and take action. EPRI has learned that there must be a lot of time spent up front to consider upgrades and understand the requirements before going in to execute upgrades.
5 - Automation and Data Collection in Power Plants
Bret Kugelmass: Are there new risks presented by going digital from a cybersecurity standpoint?
Rob Austin: Cyber systems have layers and barriers of defense. The actual protection and control systems of the plant do not have a direct internet connection and U.S. plants have no way to communicate in to those systems. The systems communicate out, but there is no interface going back in. Portable media is strictly controlled in the plant to ensure there is no malware. The information systems host the maintenance scheduling program. There is a normal corporate IT security, which utilities are very serious about. The nuclear industry has a questioning attitude and if something looks off, somebody will say something. The Electric Power Research Institute’s (EPRI) main focus in plant modernization is in applying process improvements and technology to dramatically reduce the operation and maintenance costs of an existing plant. Rob Austin has visited many non-nuclear generating plants and consistently noticed that facilities were automated and there were not many people present. Nuclear plants could be much more automated than they are right now. Maintenance could be based upon equipment conditions, utilizing sensors and wireless connectivity. EPRI’s focus in on the existing fleet, since those are the plants the U.S. has now. The key to increase operational efficiency is to risk inform the processes in the plant. This requires focusing resources effectively and applying resources to activities which are most risk-significant in the plant. Technology can be used to automate and make an operation more reliable and more effective. Permanently installed transmitters save time and effort of data collection, but there is also more information coming in about the life of the component. Information collected from the stations can be improved to better inform how they are managed going forward.
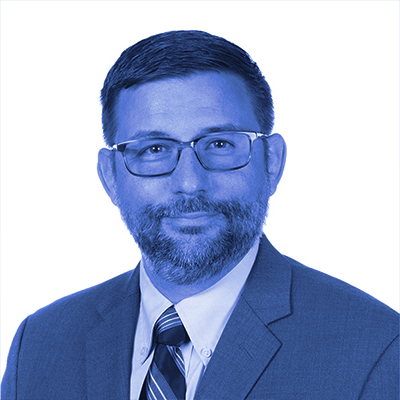
1) Dan’s background in chemical engineering and his personal journey in the nuclear industry
2) The different types of research and development an independent nonprofit organization like EPRI provides to utilities
3) Automation in the water chemistry analysis space
4) Dan’s current work providing the data necessary to qualify switching from lithium 7 to potassium hydroxide
Q1 - Water Chemistry in Nuclear Power Plants
Bret Kugelmass: How is your section of EPRI organized?
Dan Wells: Dan Wells is the water chemistry expert at the Electric Power Research Institute (EPRI), working on anything water touches at a nuclear power plant, such as water used for ultimate cooling and water that gets heated to generate electricity. Wells went to Auburn University to study chemical engineering and completed an internship at a nuclear power plant. Wells went back to university and decided he wanted to be more of a research setting than an industrial setting. Actinide work exposed him to working with radioactive materials which influence his experience and eventually got him back into nuclear energy. During graduate school, Wells did neptunium chemistry work at Argonne National Lab. He got back into nuclear in engineering support from a contracting side. As more is discovered about chemistry, it may be discovered that adding zinc to the primary coolant helps with cracking issues or adding a dispersant to the secondary side helps manage corrosion products. Most chemical addition systems are being added continually to the coolant and is monitored continuously. When you want to understand the corrosion products are in the coolant, you can hook up an apparatus to the coolant system that pulls a sample of the rust from the system for analysis. The primary chemistry that is changing over time is the oxides on the material, since metallic material corrodes over time as it is exposed to water. Chemistry is modified to slow that process, by altering the metals used and changing or purifying the coolant.
Q2 - Effects of Corrosion in Reactor Coolant
Bret Kugelmass: How do they get the water for the primary side initially?
Dan Wells: Any power plant, including nuclear power, pulls water from whatever source it is near. If it is by the sea, it may pull from a municipal source and not have to purify it as much; some plants have desalination plants on site. If the plant is on a river, the water is pulled from the river and passed through several cycles of purification until it was ready to be used as primary coolant. A pressurized water reactor has about four loops of water, each having higher purity. General corrosion releases primarily nickel and iron. When nickel goes into the core, it gets activated and turns into cobalt-58 which has a high energy gamma and produces a lot of the radiation fields in a nuclear plant. To get rid of the cobalt-58, you can purify it or reduce its deposition. High temperature water circulates quickly, so the cobalt-58 wants to go back into the water and deposit where there are heat transfer processes happening. Many plants inject zinc into the primary coolant, which competes with the cobalt-58 and gets incorporated rather than the cobalt-58. Cobalt-60 is a product of cobalt and primarily comes from an impurity in stainless steel and anytime you purify a metallic alloy. Some also comes from a high strength alloy call stellite, used in hard facings and valves. As the valves get turned, some of the cobalt comes off and gets in the coolant, getting activated and deposited. Over time, the corrosion layer between the base metals and the water gets more stable and protective. Initially you have a lot of corrosion.
Q3 - Controlling Radiation Fields
Bret Kugelmass: How has our understanding of water chemistry in reactors changed over time?
Dan Wells: If you go to a standard U.S. nuclear power plant and follow around a chemistry technician, they will be taking samples of water daily to give one data point. This requires a lot of labor and a lot of cost. Dan Wells is working on automating that process. Outside of nuclear power, a lot of plants are monitoring water and have instituted technologies that can give them a data point every 30 minutes or every hour. The Electric Power Research Institute (EPRI) is working to understand the current technologies, provide the industry with an understanding of how they operate and what the maintenance requirements are so they can get these out in the field and help with the cost requirement. If they can understand events that cause a spike in impurity or corrosion product, there is a much better chance of actively controlling the chemistry. If corrosion products are expected, you can flush the system first or send the water through the purification system. With only one data point a day, you may or may not catch the changes in corrosion products. There were some events in which primary coolant was leaking past seals that led to precipitation of boric acid outside of the primary system. Chemistry was not the fault, but chemistry was the indication. Plants have had numerous experiences with hot particles, such as a cobalt-60 particle that made it into the core and is a radiation source. The main concern is dose to the worker, which may require extra shielding or an attempt to flush the particle. Dose rate fields change how you do your work. Boric acid has a high cross-section, which describes the strength of the interaction between neutrons. In a pressurized water reactor (PWR), boric acid is used and the concentration in the system must be controlled to control fission.
Q4 - Boric Acid and Flexible Power Operation
Bret Kugelmass: How is the boric acid changing over time?
Dan Wells: Boron-10 turns generates lithium-7 in a radiochemistry process. A majority of the boric acid removal is through the purification system. In a fuel cycle, you start with fresh fuel so you need more boron to slow the fission. Over the cycle, the boric acid solution goes down through purification methods, called the boron letdown curve. Before you start a cycle, you design your boric acid letdown curve to match your core design. There are detectors monitoring the neutron flux throughout the cycle and many plants are moving towards flexible power operations, not operating at base load. This can be done by increasing the boric acid concentration, adding more to the coolant to slow down the flux, or by inserting the control rods. If you insert the control rods to slow fission and want to come back up, the core does not look the same and your boric acid can be adjusted to manage that. How quickly you can reduce power depends on where you are in the cycle, how the control rods are designed, and other factors. Changing power with chemistry takes longer and works better with lower frequencies. Boric acid is the main chemical shim used in pressurized water reactors (PWR). Western-design PWR’s add lithium to the water to manage the pH and Russian PWR’s add potassium to manage pH. The Russians also inject ammonia that decomposes to hydrogen which helps with radiolysis in the water. CANDU reactors use heavy water, which is deuterated water which also has a high cross-section for neutrons. Deuterium is used to control fission and lithium is used to control the pH. Boiling water reactors (BWR) use void fraction to control the fission, where the steam is and where the water is in the core. The density of the water impacts the fission rate and where the neutrons go. Control rods are used more frequently in BWR’s. They add zinc for radiation field reduction, but don’t have as much nickel so they don’t have as much cobalt-58. Hydrogen is also used to control radiolysis and mitigate cracking. Cracking is a concern in vessels, piping, and all internal components that are costly to replace.
Q5 - Innovation in Water Chemistry Technology
Bret Kugelmass: Are there other chemistry concerns in boiling water reactors (BWR)?
Dan Wells: There is a dryer in the top of the reactor before it goes over to the turbine, but there is still some moisture carryover in the steam. If you have water, you can carry over anything in the coolant, including the radiocobalts and end up with activity in the turbine parts of the BWR. A boiling water reactor uses almost purely water, with some zinc, in the coolant. Moving as much to automation and advanced technologies is a major initiative at the Electric Power Research Institute (EPRI). There are instruments that just sit in the flow and give you dissolved hydrogen concentration. If you want to understand nickel and iron concentration, you have a combination of dissolved species and some particulate concentration. There are a number of different technologies being applied and picking the right one for the needs of the power plant is a focus at EPRI. EPRI brings an assembly of instruments to plants to demonstrate new technologies. This lets EPRI know how the technologies work in the environment they need them to work and also determine maintenance requirements. Quality assurance programs are the main thing driving maintenance requirements. Regulatory space for water chemistry is pretty light in the U.S., but is very country dependent. Boric acid is included in the design for fission and lithium is included for pH, but no other chemistry is included in U.S. regulatory documents. EPRI has a set of water chemistry guidelines developed and updated by the industry based on R&D and the utilities have committed to meeting the guidelines. This document includes action levels and sampling and monitoring frequencies.
Q6 - Automated Chemistry Control
Bret Kugelmass: What other type of R&D activities does EPRI engage in?
Dan Wells: In addition to the kind of analysis technologies, the water chemistry department at the Electric Power Research Institute (EPRI) has started an initiative working on advanced data analytics. EPRI has a software package of data analytics that continually analyzes the plant data and sends alert to check on parameters. With much better data, EPRI is working to develop better algorithms to analyze the data and make the analysis even more automated. Advanced plants and small modular reactors (SMR) have automated chemistry monitoring and control in their designs. For a parameter like pH where you are trying to keep it in a range, a purification bed could come on to help remove lithium, then later the purification bed could be removed from the system. Algorithms are analyzing that data continually to look for issues and changes in control and the actual plant maneuvers to that data. Different molten salt coolants change the type of analysis you want to do. Understanding the chemistry of molten salt is not determined at all and the materials have not been finalized yet. EPRI has not historically worked in the gas-cooled reactor space as it relates to water chemistry. There are issues with purifying lithium-7, so EPRI is doing work to qualify that it would be safe to switch from lithium to potassium, which could bring a lot of potential savings. EPRI is also looking into film forming products that help provide another impediment to water corrosion, which would eliminate having to mediate the other issues down the line. The fossil fleet already has automated chemistry. The technologies are there to close the gaps in nuclear and reduce the overall cost of operating the plant.
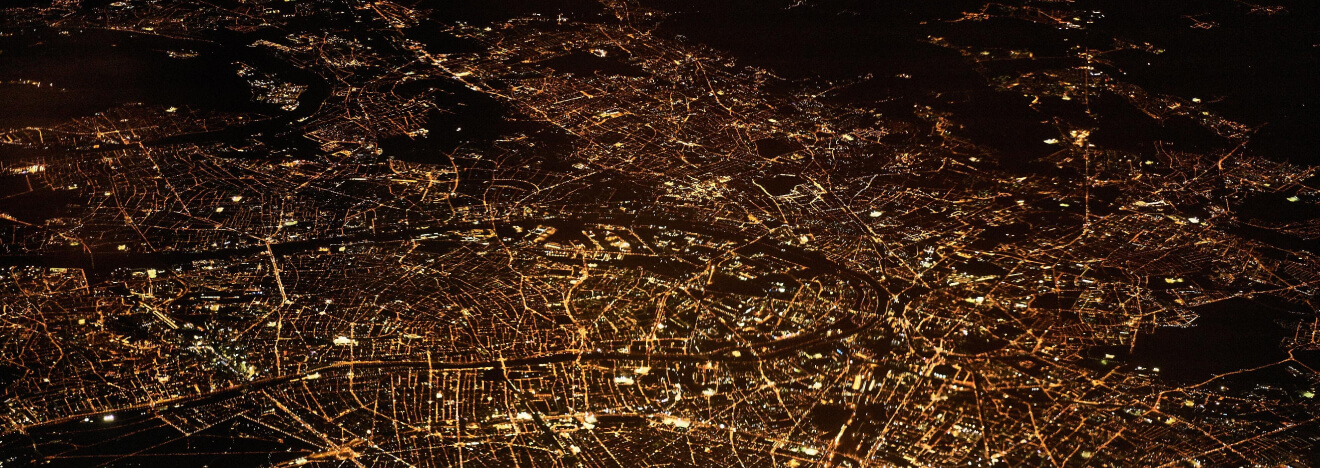
Sign up for our newsletter
No results found
Please try different keywords